Precision machining is at the core of modern manufacturing, particularly for industries that demand tight tolerances and high-quality finishes. The integration of live tooling and a Y-axis in CNC lathes has revolutionized the production of mill-turned parts, allowing for greater efficiency, improved accuracy, and enhanced quality control. The images provided showcase real-world examples of precision-machined components and the meticulous inspection processes that ensure they meet exact specifications.
The Advantages of Live Tooling and Y-Axis in CNC Lathes
Traditionally, turned parts required secondary operations on a milling machine to add features such as holes, slots, or keyways. However, modern CNC lathes equipped with live tooling and a Y-axis eliminate the need for these extra steps, offering significant benefits:
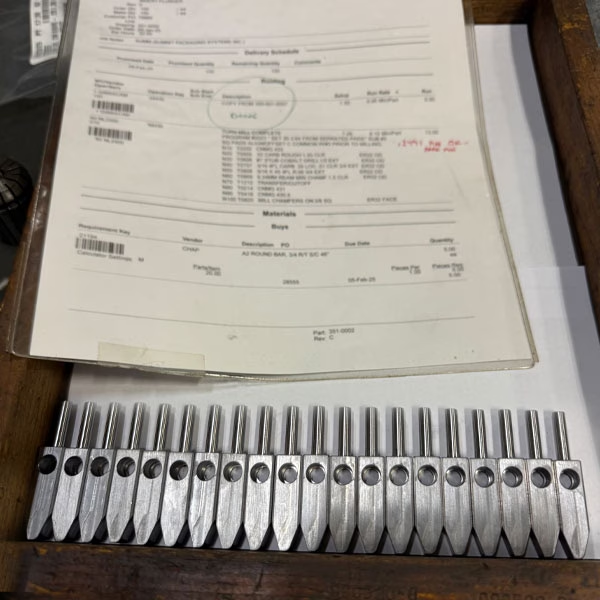
1. Reduced Setup Time and Increased Efficiency
With live tooling, machining centers can perform milling, drilling, and tapping operations directly on the lathe, reducing the number of times a part needs to be moved between machines. The addition of a Y-axis allows for more complex geometries to be completed in a single setup.
Example from the image: The precisely machined aluminum components illustrate how a single-machine process ensures uniform hole patterns and milled features, reducing variability caused by repositioning parts between different machines.
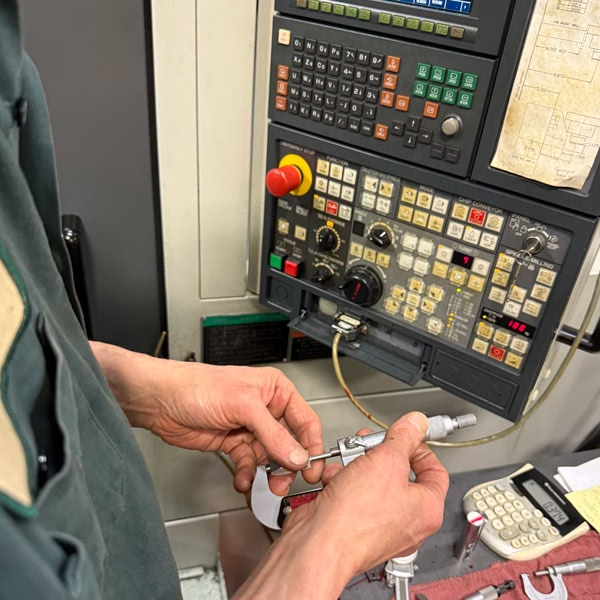
2. Improved Accuracy and Consistency
Each time a part is transferred between machines, there is a risk of misalignment and dimensional inconsistencies. By keeping all machining operations in one place, CNC lathes with Y-axis capabilities maintain tighter tolerances and better repeatability.
Example from the image: The skilled machinist is seen using a micrometer to verify the dimensions of a turned component. This step is crucial for ensuring that all features remain within the specified tolerances, especially when working with complex geometries made possible by Y-axis movements.
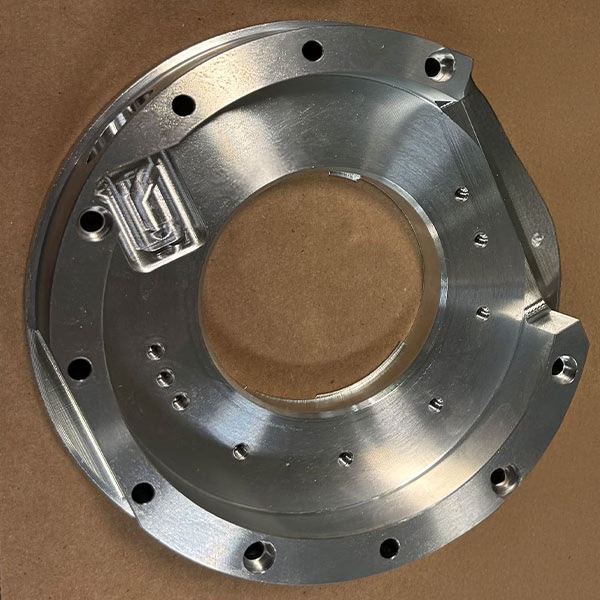
3. Superior Surface Finish and Quality Control
Live tooling reduces the number of times a part needs to be clamped, which in turn minimizes potential defects from misalignment or tool marks. The ability to machine multiple features in one pass also ensures smoother transitions between turned and milled surfaces.
Example from the image: The organized set of small precision-machined parts, neatly aligned and inspected with detailed job documentation, highlights the importance of quality control in high-precision manufacturing. These parts benefit from multi-axis machining, which ensures accurate dimensions and high-quality finishes.
Conclusion
Investing in CNC lathes with live tooling and a Y-axis is a game-changer for manufacturers looking to improve efficiency, accuracy, and quality control. The images provided give a clear view of how advanced machining techniques contribute to the production of high-quality mill-turned parts, eliminating unnecessary secondary operations and ensuring consistent precision.
By leveraging these technologies, machine shops can reduce lead times, lower production costs, and maintain stringent quality standards, making them more competitive in today’s demanding industries. Ready to optimize your production process? Contact VertX Manufacturing today to see how our cutting-edge machining solutions can support your needs!